Công nghệ in 3D đã và đang tạo ra một cuộc cách mạng trong ngành sản xuất với những ưu điểm vượt trội như tốc độ sản xuất nhanh, thiết kế linh hoạt, tiết kiệm chi phí và tính sáng tạo cao.
Tuy nhiên, những hạn chế về chất lượng sản phẩm, giới hạn vật liệu, chi phí đầu tư ban đầu và khả năng sản xuất hàng loạt vẫn là những thách thức cần giải quyết.
1. Khát quát về in 3D và các lợi ích
Công nghệ in 3D (hay còn gọi là chế tạo đắp lớp) là quá trình tạo ra các vật thể ba chiều từ mô hình số hóa bằng cách xếp chồng các lớp vật liệu lên nhau. Khác với phương pháp chế tạo truyền thống vốn loại bỏ vật liệu, in 3D hoạt động theo nguyên lý đắp thêm vật liệu theo từng lớp.
Quy trình bắt đầu từ việc thiết kế mô hình 3D trên máy tính, sau đó phần mềm chuyên dụng sẽ cắt mô hình thành nhiều lớp mỏng và gửi hướng dẫn đến máy in. Công nghệ này đã mở ra thời đại mới cho ngành sản xuất với khả năng tạo ra các thiết kế phức tạp mà phương pháp truyền thống khó thực hiện.
Một trong những lợi ích lớn nhất của công nghệ in 3D là khả năng hiện thực hóa những ý tưởng thiết kế phức tạp và độc đáo, điều mà các phương pháp sản xuất truyền thống khó có thể đạt được.
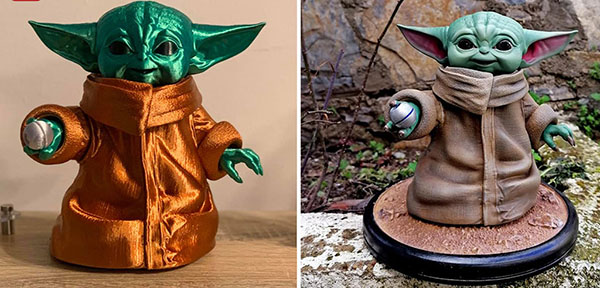
Với in 3D, các nhà thiết kế và kỹ sư không còn bị giới hạn bởi các quy tắc và ràng buộc của quy trình sản xuất thông thường. Bất kỳ ai có ý tưởng và kỹ năng thiết kế đều có thể tạo ra sản phẩm của riêng mình, từ đồ trang trí cá nhân hóa đến các bộ phận kỹ thuật chuyên dụng.
So với các phương pháp sản xuất truyền thống như đúc, gia công hoặc ép phun, in 3D có thể giảm đáng kể thời gian sản xuất. Quá trình in 3D diễn ra tự động và liên tục, cho phép tạo ra sản phẩm trong vài giờ hoặc thậm chí vài phút, tùy thuộc vào kích thước và độ phức tạp của thiết kế.
Ví dụ, các công ty sản xuất ô tô có thể sử dụng in 3D để tạo mẫu các bộ phận mới một cách nhanh chóng, giúp họ thử nghiệm và cải tiến thiết kế một cách linh hoạt. Bên cạnh đó, công nghệ in 3D hiện đại có thể đạt được độ chính xác rất cao, đảm bảo rằng sản phẩm cuối cùng đáp ứng các yêu cầu kỹ thuật khắt khe.
Ngoài những lợi ích chính đã nêu, công nghệ in 3D còn mang lại nhiều ưu điểm khác, như:
- Sản xuất theo yêu cầu: In 3D cho phép sản xuất các sản phẩm theo yêu cầu của khách hàng, đáp ứng nhu cầu cá nhân hóa ngày càng cao.
- Sản xuất tại chỗ: In 3D có thể được sử dụng để sản xuất các sản phẩm tại chỗ, giảm chi phí vận chuyển và thời gian giao hàng.
- Tạo ra các sản phẩm phức tạp: In 3D có thể tạo ra các sản phẩm có hình dạng phức tạp và cấu trúc bên trong rỗng, điều mà các phương pháp sản xuất truyền thống khó có thể thực hiện được.
2. Ưu điểm của công nghệ in 3D
2.1. Tốc độ sản xuất nhanh
Công nghệ in 3D giúp rút ngắn đáng kể thời gian từ ý tưởng đến sản phẩm hoàn chỉnh. Trong quy trình phát triển sản phẩm truyền thống, việc tạo mẫu thử có thể mất từ vài tuần đến vài tháng, bao gồm thiết kế, chế tạo khuôn, đúc và hoàn thiện. Với in 3D, thời gian này được rút ngắn xuống chỉ còn vài giờ hoặc vài ngày.
Ví dụ cụ thể, công ty Ford đã giảm thời gian phát triển các bộ phận động cơ từ 4-5 tháng xuống chỉ còn 3 ngày nhờ sử dụng công nghệ in 3D để tạo mẫu thử. Tương tự, trong ngành y tế, việc tạo ra các mô hình giải phẫu tùy chỉnh cho bệnh nhân trước khi phẫu thuật chỉ mất vài ngày thay vì vài tuần.
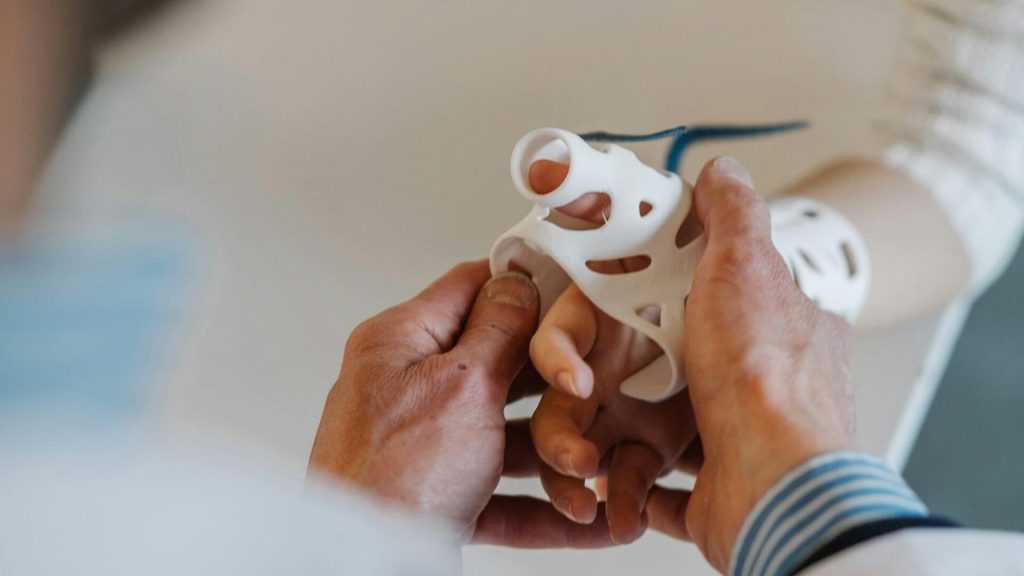
Khả năng cập nhật và điều chỉnh thiết kế nhanh chóng cũng là một lợi thế lớn. Khi phát hiện lỗi hoặc cần cải tiến, nhà thiết kế chỉ cần sửa đổi file CAD và in lại mẫu mới, thay vì phải làm lại toàn bộ quy trình chế tạo phức tạp.
2.2. Thiết kế linh hoạt
Một trong những ưu điểm nổi bật nhất của công nghệ in 3D là khả năng tạo ra các hình dạng phức tạp mà phương pháp sản xuất truyền thống không thể thực hiện được. In 3D có thể tạo ra các cấu trúc rỗng bên trong, các đường cong phức tạp, và các chi tiết tinh xảo mà không cần đến công đoạn lắp ráp.
Ví dụ, ngành hàng không đã sử dụng in 3D để tạo ra các bộ phận có cấu trúc tổ ong bên trong, giúp giảm trọng lượng đến 70% nhưng vẫn đảm bảo độ bền. Trong ngành y tế, các implant tùy chỉnh phù hợp với giải phẫu của từng bệnh nhân được tạo ra dễ dàng, như khớp háng hoặc xương hàm nhân tạo vừa khít với cơ thể người nhận.
Khả năng tạo ra các bộ phận phức tạp trong một lần in cũng giúp giảm số lượng chi tiết cần lắp ráp, từ đó giảm thiểu rủi ro hỏng hóc và tăng độ bền của sản phẩm.
2.3. Tiết kiệm chi phí
In 3D giúp tiết kiệm chi phí sản xuất thông qua nhiều cách:
- Giảm lãng phí vật liệu: Khác với phương pháp cắt gọt truyền thống có thể lãng phí đến 90% vật liệu, in 3D chỉ sử dụng đúng lượng vật liệu cần thiết.
- Không cần khuôn mẫu: Việc tạo khuôn cho sản xuất truyền thống có thể tốn từ hàng nghìn đến hàng chục nghìn đô la. In 3D loại bỏ hoàn toàn chi phí này.
- Giảm chi phí lắp ráp: Khả năng in các bộ phận phức tạp trong một lần giúp giảm số lượng chi tiết cần lắp ráp, từ đó giảm chi phí nhân công.
Ví dụ cụ thể, GE Aviation đã sử dụng in 3D để sản xuất đầu phun nhiên liệu cho động cơ máy bay, giúp giảm 30% chi phí sản xuất và tăng 5 lần tuổi thọ sản phẩm. Trong lĩnh vực nha khoa, việc sử dụng máy in 3D để tạo ra các mẫu hàm giả giúp giảm chi phí đến 80% so với phương pháp truyền thống.
2.4. Tính sáng tạo cao
Công nghệ in 3D mở ra khả năng hiện thực hóa những ý tưởng thiết kế mà trước đây không thể thực hiện được. Nhà thiết kế không còn bị giới hạn bởi những ràng buộc của phương pháp sản xuất truyền thống.
Trong lĩnh vực thời trang, nhà thiết kế Iris van Herpen đã tạo ra những bộ trang phục với cấu trúc phức tạp không thể thực hiện bằng phương pháp may truyền thống. Trong kiến trúc, các mô hình kiến trúc phức tạp với đường cong tự nhiên được tạo ra dễ dàng, giúp kiến trúc sư thể hiện tầm nhìn sáng tạo của mình một cách trọn vẹn.
Công nghệ in 3D cũng cho phép cá nhân hóa sản phẩm ở mức độ cao, từ đế giày tùy chỉnh theo dáng bàn chân đến đồ trang sức với thiết kế độc đáo cho từng khách hàng.
3. Nhược điểm của công nghệ in 3D
3.1. Chất lượng sản phẩm
Mặc dù công nghệ in 3D không ngừng phát triển, chất lượng sản phẩm in 3D vẫn còn một số hạn chế so với phương pháp sản xuất truyền thống:
- Độ chính xác và độ phân giải: Sản phẩm in 3D thường có đường nét “bậc thang” do quá trình đắp lớp, đặc biệt là với các máy in giá rẻ. Trong khi các phương pháp như CNC có thể đạt độ chính xác đến 0.001mm, nhiều máy in 3D phổ thông chỉ đạt độ chính xác khoảng 0.1mm.
- Độ bền cơ học: Các sản phẩm in FDM thường có cấu trúc dạng lớp nên dễ bị gãy theo phương ngang. Trong khi đó, các sản phẩm đúc hoặc gia công cơ khí có độ bền đồng nhất theo mọi hướng.
- Hoàn thiện bề mặt: Sản phẩm in 3D thường cần xử lý sau in như mài nhẵn, sơn phủ để có bề mặt mịn như sản phẩm truyền thống.
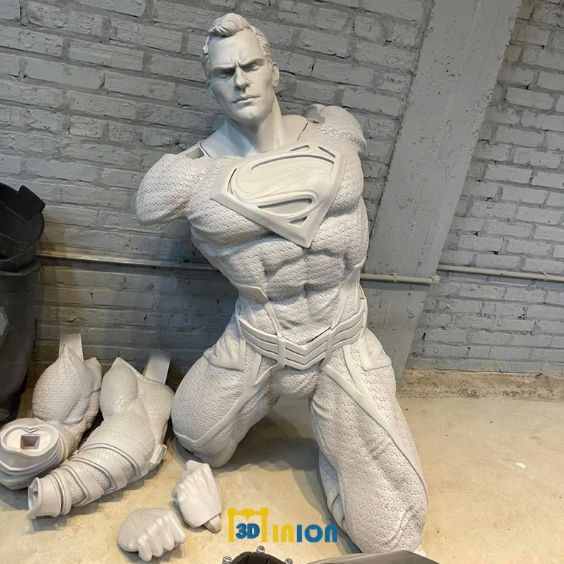
Ví dụ, trong ngành công nghiệp ô tô, các bộ phận chịu lực quan trọng vẫn được sản xuất bằng phương pháp truyền thống vì yêu cầu cao về độ bền và độ tin cậy. Các chi tiết in 3D chủ yếu được sử dụng cho mục đích trang trí hoặc các bộ phận không chịu lực.
3.2. Giới hạn vật liệu
Mặc dù danh sách vật liệu in 3D ngày càng mở rộng, số lượng và loại vật liệu có thể sử dụng vẫn còn hạn chế so với phương pháp sản xuất truyền thống:
- Số lượng vật liệu: Trong khi phương pháp truyền thống có thể sử dụng hàng nghìn loại vật liệu khác nhau, in 3D hiện chỉ có khoảng vài trăm loại vật liệu phù hợp.
- Chất lượng vật liệu: Nhiều vật liệu in 3D có đặc tính cơ học và độ bền kém hơn so với vật liệu truyền thống cùng loại.
- Chi phí vật liệu: Vật liệu in 3D thường đắt hơn 2-10 lần so với vật liệu thông thường cùng loại.
Ví dụ, filament nhựa PLA phổ biến trong in FDM có giá khoảng 20-50 USD/kg, trong khi hạt nhựa PLA nguyên liệu chỉ có giá 2-3 USD/kg. Tương tự, bột kim loại cho in SLS có giá từ 300-500 USD/kg, cao hơn nhiều so với kim loại thông thường.
Giới hạn về vật liệu cũng ảnh hưởng đến khả năng ứng dụng, đặc biệt trong các ngành yêu cầu vật liệu đặc biệt như hàng không vũ trụ hoặc y tế.
3.3. Chi phí đầu tư ban đầu
Mặc dù giá máy in 3D đã giảm đáng kể trong những năm gần đây, chi phí đầu tư ban đầu vẫn là một rào cản lớn:
- Chi phí máy móc: Máy in 3D công nghiệp chất lượng cao có giá từ vài chục nghìn đến hàng triệu USD. Máy in kim loại SLM có thể có giá từ 500.000 USD trở lên.
- Chi phí phần mềm: Phần mềm thiết kế CAD chuyên nghiệp và phần mềm xử lý cho in 3D có thể tốn từ vài nghìn đến hàng chục nghìn USD mỗi năm.
- Chi phí đào tạo: Nhân viên cần được đào tạo để sử dụng hiệu quả công nghệ in 3D, từ thiết kế đến vận hành máy và xử lý sau in.
Ví dụ, một hệ thống in SLA công nghiệp từ Formlabs có thể có giá khoảng 10.000 USD, trong khi một máy in kim loại từ EOS có thể lên đến 1 triệu USD. Ngoài ra còn phải tính đến chi phí bảo trì, điện năng, không gian làm việc và hệ thống an toàn.
Đối với các doanh nghiệp nhỏ, việc tính toán thời gian hoàn vốn (ROI) là rất quan trọng khi quyết định đầu tư vào công nghệ in 3D.
3.4. Sản xuất hàng loạt
In 3D vẫn còn nhiều hạn chế trong sản xuất quy mô lớn:
- Tốc độ in chậm: Quá trình in 3D có thể mất từ vài giờ đến vài ngày cho một sản phẩm, trong khi các phương pháp như đúc ép có thể sản xuất hàng trăm sản phẩm mỗi giờ.
- Quy mô giới hạn: Kích thước sản phẩm bị giới hạn bởi kích thước buồng in của máy in 3D.
- Chi phí đơn vị cao: Với số lượng lớn (>10.000 đơn vị), chi phí sản xuất bằng phương pháp truyền thống thường thấp hơn nhiều so với in 3D.
Ví dụ, một nhà máy sản xuất đồ chơi bằng phương pháp đúc ép có thể tạo ra 10.000 chi tiết nhựa mỗi ngày, trong khi một trang trại máy in 3D với 100 máy in FDM chỉ có thể sản xuất khoảng 1.000 chi tiết tương tự mỗi ngày.
Các công ty lớn như Adidas đã thử nghiệm sản xuất giày bằng in 3D, nhưng vẫn giới hạn ở các dòng sản phẩm cao cấp, số lượng nhỏ vì chi phí sản xuất cao hơn nhiều so với phương pháp truyền thống.
4. Các loại công nghệ in 3D
Dưới đây là bảng so sánh ưu nhược điểm của 3 loại công nghệ in 3D phổ biến nhất hiện nay:
Công nghệ | Nguyên lý hoạt động | Ưu điểm | Nhược điểm |
FDM (Fused Deposition Modeling) | Nóng chảy và đùn nhựa theo từng lớp.
Đầu phun di chuyển theo hướng X-Y, trong khi bàn in di chuyển theo hướng Z. |
– Chi phí thấp nhất – Dễ sử dụng và bảo trì – Đa dạng vật liệu nhựa – Phù hợp cho văn phòng |
– Độ phân giải thấp (0.1-0.3mm) – Bề mặt thô, có đường vân – Cường độ yếu theo phương Z – Tốc độ in chậm với chi tiết phức tạp |
SLA (Stereolithography) | Sử dụng tia laser hoặc đèn UV để làm cứng nhựa resin lỏng theo từng lớp. Bàn in nâng lên sau mỗi lớp được in. | – Độ phân giải cao (0.025-0.05mm) – Bề mặt mịn, chi tiết tinh xảo – Phù hợp cho trang sức, nha khoa – Tốc độ in nhanh hơn FDM |
– Chi phí cao hơn FDM – Vật liệu giòn, dễ gãy – Cần xử lý sau in (rửa, phơi UV) – Resin độc hại, cần thông gió tốt |
SLS (Selective Laser Sintering) | Sử dụng tia laser công suất cao để nung chảy và kết dính bột nhựa hoặc kim loại theo từng lớp. Sau mỗi lớp, bột mới được phủ lên. | – Không cần cấu trúc đỡ – Sản phẩm có độ bền cao – Phù hợp cho chế tạo chức năng – Có thể in kim loại, gốm sứ |
– Chi phí rất cao – Yêu cầu không gian lớn – Tiêu thụ năng lượng cao – Bề mặt xốp, cần xử lý sau in |
Công nghệ in 3D đã và đang tạo ra một cuộc cách mạng trong ngành sản xuất với những ưu điểm vượt trội như tốc độ sản xuất nhanh, thiết kế linh hoạt, tiết kiệm chi phí và tính sáng tạo cao. Tuy nhiên, những hạn chế về chất lượng sản phẩm, giới hạn vật liệu, chi phí đầu tư ban đầu và khả năng sản xuất hàng loạt vẫn là những thách thức cần giải quyết.
Trong tương lai, công nghệ in 3D được dự đoán sẽ phát triển mạnh mẽ với việc ra đời các vật liệu mới, cải tiến tốc độ in và độ chính xác. Ngành y tế đang chứng kiến những bước tiến đáng kể với khả năng in mô và cơ quan nhân tạo. Trong công nghiệp, việc kết hợp in 3D với tự động hóa và trí tuệ nhân tạo đang mở ra khả năng sản xuất theo yêu cầu, giảm thiểu tồn kho và tối ưu hóa chuỗi cung ứng.
Các ứng dụng thực tế của in 3D đã xuất hiện trong nhiều lĩnh vực. Trong y tế, các bác sĩ đã sử dụng mô hình in 3D để lập kế hoạch phẫu thuật phức tạp và tạo ra implant tùy chỉnh. Trong xây dựng, công ty ICON đã thử nghiệm in 3D các ngôi nhà hoàn chỉnh trong vòng 24 giờ với chi phí thấp, mở ra tiềm năng giải quyết khủng hoảng nhà ở toàn cầu.