Bài viết dưới đây sẽ phân tích chi tiết cơ chế chiếu ánh sáng DLP, vai trò của chip DMD và quá trình quang trùng hợp nhựa đồng thời giúp bạn so sánh chuyên sâu giữa các công nghệ in resin (SLA, DLP, LCD) với bảng đối chiếu đầy đủ về độ phân giải, tốc độ và chi phí. 3D Minion sẽ giúp bạn hiểu sâu về công nghệ in 3D DLP và gợi ý chọn máy in DLP phù hợp với nhu cầu và ngân sách.
1. Bản chất công nghệ in 3D DLP là gì?
Công nghệ in 3D DLP (Digital Light Processing) là kỹ thuật in 3D tiên tiến sử dụng ánh sáng để làm cứng nhựa lỏng (resin) theo từng lớp, tạo nên mô hình 3D chi tiết và chính xác. Đây là một trong những phương pháp in 3D dựa trên nguyên lý quang trùng hợp (photopolymerization), được phát triển bởi Texas Instruments vào thập niên 1980.
Nguyên lý của kỹ thuật in 3D DLP có thể giải thích đơn giản như sau:
Công nghệ DLP sử dụng nguồn ánh sáng chiếu qua một chip vi điện tử có hàng triệu gương siêu nhỏ được gọi là DMD (Digital Micromirror Device). Mỗi gương tương ứng với một điểm ảnh (pixel) trên hình chiếu. Ánh sáng, thường là tia UV hoặc ánh sáng xanh có bước sóng cụ thể, được chiếu lên toàn bộ mặt phẳng lớp nhựa cùng một lúc. Điều này tạo ra hiệu ứng “chiếu rọi” toàn bộ lớp mô hình trong một lần, khác biệt so với công nghệ SLA sử dụng laser quét từng điểm.
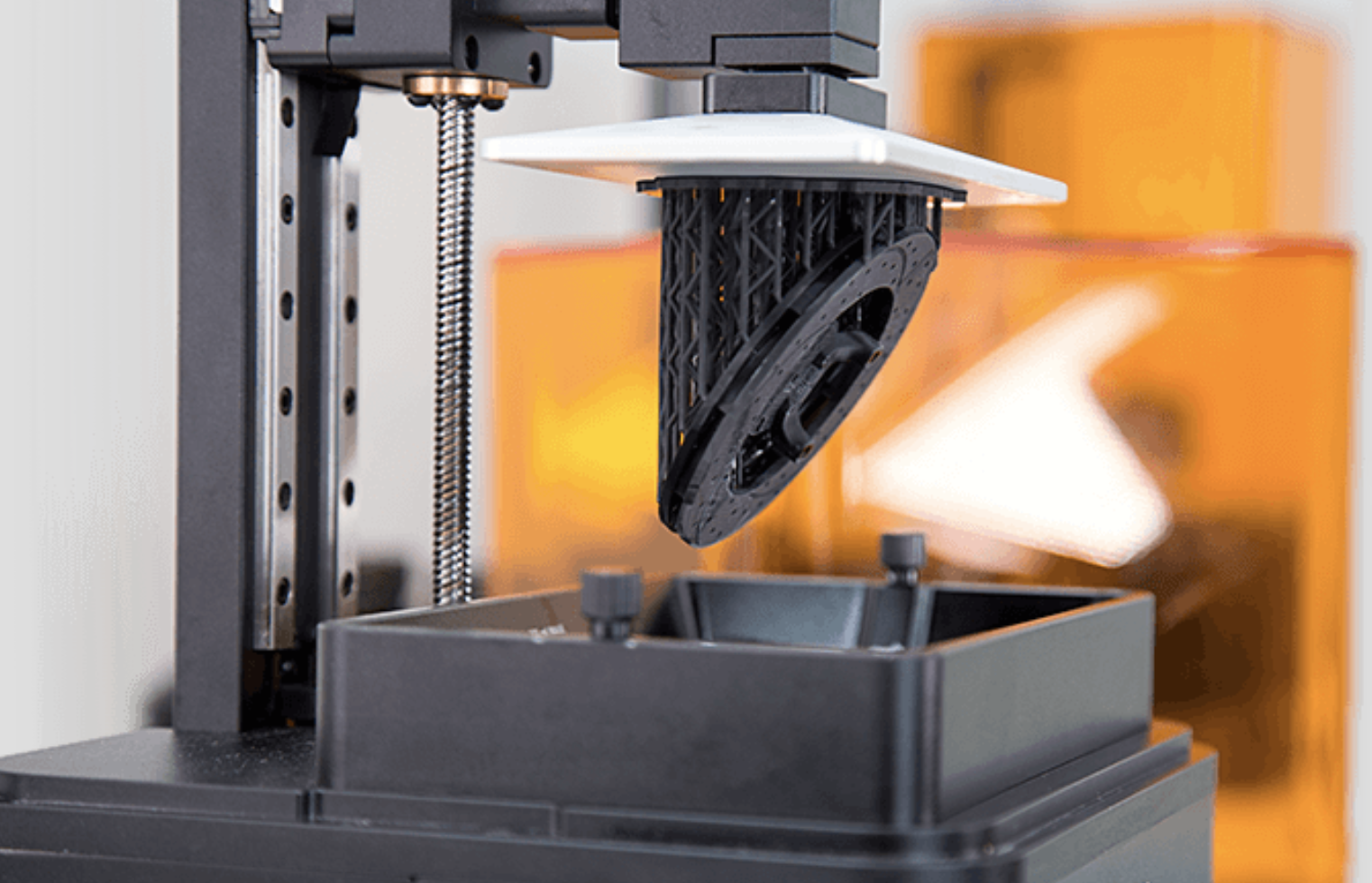
Chip DMD là thành phần quan trọng nhất trong máy in 3D DLP. Chip này bao gồm hàng triệu gương vi cơ (micromirrors) có kích thước chỉ vài micromet. Mỗi gương có thể được điều khiển nghiêng ±10-12 độ để phản xạ ánh sáng theo hai hướng:
- Hướng “ON”: Phản xạ ánh sáng đến bề mặt nhựa, kích hoạt phản ứng đông cứng
- Hướng “OFF”: Phản xạ ánh sáng ra khỏi bề mặt nhựa, không gây phản ứng
Việc điều khiển các gương vi mô này được thực hiện với tốc độ cực nhanh (hàng nghìn lần/giây), cho phép tạo ra các điểm ảnh rất chính xác và sắc nét. Độ phân giải của mô hình phụ thuộc trực tiếp vào số lượng gương trong chip DMD, thường dao động từ 1080p đến 4K trong các máy in hiện đại.
Khi ánh sáng UV chiếu vào nhựa lỏng (photopolymer resin), nó kích hoạt các chất khơi mào (photoinitiators) trong nhựa, bắt đầu phản ứng quang trùng hợp. Phản ứng này biến đổi nhựa lỏng thành polymer rắn theo hình dạng chính xác của mẫu thiết kế. Quá trình này diễn ra như sau:
- Ánh sáng UV kích hoạt các phân tử khơi mào trong nhựa
- Các phân tử khơi mào tạo ra các gốc tự do (free radicals)
- Gốc tự do kích hoạt phản ứng trùng hợp chuỗi, liên kết các đơn phân (monomers) thành polymer
- Polymer hình thành mạng lưới 3D rắn theo hình dạng được chiếu
Quá trình trùng hợp diễn ra nhanh chóng, thường trong vài giây đến vài phút tùy thuộc vào loại nhựa và cường độ ánh sáng. Sau khi một lớp được in xong, bàn đỡ di chuyển lên hoặc xuống (tùy vào thiết kế máy), tạo khoảng trống cho lớp nhựa mới, và quá trình chiếu lặp lại cho lớp tiếp theo.
2. Ưu-nhược điểm của công nghệ in 3D DLP
2.1. Ưu điểm:
- Tốc độ in nhanh: Nhờ vào việc chiếu sáng cả một lớp cùng lúc, DLP nhanh hơn đáng kể so với công nghệ SLA dùng laser quét từng điểm. Thời gian in của DLP có thể nhanh hơn 5-10 lần so với SLA đối với cùng một mô hình.
- Độ phân giải cao: Công nghệ DLP cho phép in các chi tiết mịn với độ phân giải có thể đạt đến 25-50 micron (0.025-0.05mm) trên trục XY, tùy thuộc vào chất lượng của chip DMD và hệ thống quang học.
- Chi phí vận hành thấp: So với các công nghệ in 3D khác như SLS hay SLM, chi phí vận hành của DLP thấp hơn nhờ nguồn sáng LED có tuổi thọ cao và tiêu thụ ít điện năng hơn các hệ thống laser công suất cao.
- Bề mặt mịn: Sản phẩm in DLP có bề mặt mịn màng với ít dấu vết của các lớp in, giảm thiểu nhu cầu xử lý sau in, đặc biệt lý tưởng cho các ứng dụng yêu cầu thẩm mỹ cao như nha khoa hay đồ trang sức.
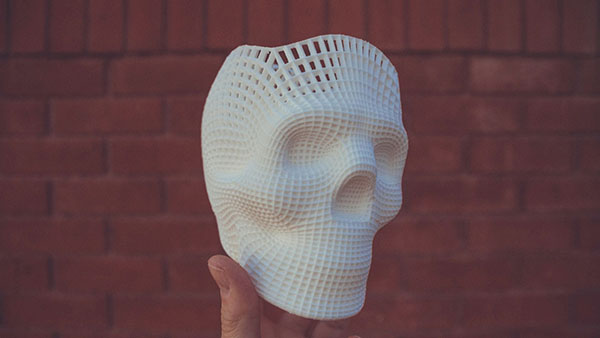
2.2. Nhược điểm:
- Giá thiết bị cao: Máy in DLP chất lượng cao với độ phân giải và độ chính xác tốt thường có giá từ 3,000 đến 10,000 USD, cao hơn so với nhiều loại máy in FDM cơ bản.
- Giới hạn kích thước: Vùng in của máy DLP thường nhỏ hơn so với các công nghệ khác, với kích thước điển hình từ 90x50x150mm đến 192x120x200mm. Điều này hạn chế khả năng in các vật thể lớn.
- Yêu cầu hậu xử lý: Sau khi in, sản phẩm cần được rửa sạch nhựa dư thừa bằng cồn isopropyl (IPA) hoặc các dung môi khác, sau đó phải được gia cố bằng tia UV để đạt độ cứng và độ bền tối ưu.
- Vật liệu đặc thù: DLP yêu cầu sử dụng nhựa quang trùng hợp đặc biệt, thường đắt hơn 3-5 lần so với filament dùng cho máy in FDM. Ngoài ra, nhựa này có thể gây kích ứng da và cần được xử lý cẩn thận.
2.3. Giải pháp:
- Cách tối ưu quy trình:
- Điều chỉnh thời gian chiếu sáng (exposure time) phù hợp với từng loại nhựa
- Sử dụng phần mềm slicing chuyên dụng có khả năng tối ưu hóa cấu trúc đỡ
- Định hướng mô hình hợp lý để giảm thiểu diện tích cần cấu trúc đỡ
- Thực hiện bảo trì định kỳ cho thùng nhựa và màng FEP để tránh lỗi in
- Lựa chọn vật liệu phù hợp:
- Sử dụng nhựa chuyên dụng cho từng ứng dụng (như nhựa dental cho nha khoa, nhựa castable cho đúc trang sức)
- Chọn nhựa có độ nhớt phù hợp với độ phân giải mong muốn
- Bảo quản nhựa đúng cách trong hộp kín, tránh ánh sáng để kéo dài tuổi thọ
- Cân nhắc sử dụng nhựa thân thiện với môi trường cho các ứng dụng không yêu cầu đặc tính cơ học cao
- Kỹ thuật hậu xử lý:
- Thiết lập quy trình rửa 2 bước: rửa sơ bộ và rửa chính
- Sử dụng thiết bị rửa siêu âm để làm sạch các khe hở và chi tiết phức tạp
- Gia cố UV trong môi trường không oxy (trong nước hoặc buồng nitơ) để tránh hiện tượng ức chế oxy
- Phủ lớp bảo vệ như sơn acrylic hoặc epoxy để tăng độ bền và tuổi thọ sản phẩm
3. Quy trình in 3D DLP và các dòng máy in phù hợp
3.1 Quy trình in 3D DLP
Chuẩn bị:
Kiểm tra thiết bị:
- Vệ sinh thùng nhựa và kiểm tra màng FEP xem có bị xước hoặc hư hỏng
- Kiểm tra bề mặt bàn đỡ đảm bảo phẳng và sạch
- Kiểm tra hệ thống quang học, làm sạch các bề mặt phản xạ và thấu kính
- Cân chỉnh bàn đỡ để đảm bảo song song với mặt phẳng chiếu sáng
Việc kiểm tra thiết bị trước khi in rất quan trọng vì nó giúp ngăn ngừa các lỗi in phổ biến như bám dính kém hoặc biến dạng. Đặc biệt, tình trạng của màng FEP (lớp trong suốt ở đáy thùng nhựa) có ảnh hưởng trực tiếp đến chất lượng in.
Cài đặt phần mềm:
- Cập nhật firmware của máy in lên phiên bản mới nhất
- Cài đặt phần mềm slicing chuyên dụng như ChiTuBox, Lychee Slicer hoặc PrusaSlicer
- Tải và cài đặt profile phù hợp với loại nhựa sẽ sử dụng
- Thiết lập kết nối giữa máy tính và máy in (qua USB, Wi-Fi hoặc mạng LAN)
Phần mềm slicing đóng vai trò quan trọng trong việc chuyển đổi mô hình 3D thành các lớp 2D và tạo cấu trúc đỡ. Việc sử dụng profile phù hợp với từng loại nhựa giúp tối ưu hóa thời gian chiếu sáng và độ bám dính giữa các lớp.
Chuẩn bị mô hình 3D:
- Kiểm tra và sửa lỗi trên mô hình 3D (non-manifold edges, lỗ hổng)
- Điều chỉnh kích thước mô hình phù hợp với vùng in
- Định hướng mô hình để giảm thiểu lực kéo và nhu cầu cấu trúc đỡ
- Tối ưu hóa độ dày của các bức tường và chi tiết phù hợp với khả năng của máy in
Chất lượng của file STL/OBJ ban đầu ảnh hưởng lớn đến kết quả in. Các mô hình không kín (non-watertight) có thể gây ra lỗi trong quá trình slicing và in.
Chuẩn bị vật liệu in:
- Lắc đều nhựa in để đảm bảo các thành phần được trộn đều
- Lọc nhựa qua lưới lọc mịn (thường 50-100 micron) để loại bỏ các mảnh đã đông cứng
- Đổ nhựa vào thùng đến mức khuyến nghị (thường khoảng 1/3 đến 1/2 chiều cao)
- Để nhựa ổn định vài phút để các bọt khí thoát ra
Việc khuấy trộn nhựa đúng cách đảm bảo các chất phụ gia và chất khơi mào được phân bố đều, giúp phản ứng quang trùng hợp diễn ra đồng đều trên toàn bộ mô hình.
Các bước tiến hành quy trình in:
Slicing mô hình:
- Nhập mô hình 3D vào phần mềm slicing
- Thêm cấu trúc đỡ (supports) tự động hoặc thủ công
- Thiết lập độ dày lớp (thường từ 0.025mm đến 0.1mm)
- Xuất file đã sliced sang định dạng tương thích với máy in (thường là .ctb, .photon hoặc .sl1)
Quá trình slicing chia mô hình thành các lớp mỏng, đồng thời tạo ra các cấu trúc đỡ cần thiết. Độ dày lớp ảnh hưởng trực tiếp đến độ chi tiết và thời gian in.
Cài đặt thông số:
- Thiết lập thời gian chiếu sáng cho các lớp đáy (thường 30-60 giây)
- Thiết lập thời gian chiếu sáng cho các lớp thường (thường 2-10 giây)
- Cài đặt tốc độ nâng và hạ của bàn đỡ (thường 60-180mm/phút)
- Thiết lập khoảng cách nâng giữa các lớp (thường 5-8mm)
Các thông số in phải được điều chỉnh phù hợp với loại nhựa, độ dày lớp và nhiệt độ môi trường. Thời gian chiếu sáng quá ngắn có thể dẫn đến bám dính kém, trong khi thời gian quá dài có thể gây biến dạng và mất chi tiết.
Kiểm tra căn chỉnh:
- Thực hiện căn chỉnh bàn đỡ (leveling) theo hướng dẫn của nhà sản xuất
- Đảm bảo khoảng cách giữa bàn đỡ và đáy thùng nhựa chính xác (thường bằng một tờ giấy)
- Kiểm tra lực bám dính ban đầu thông qua thử nghiệm in lớp đáy
- Đảm bảo máy in được đặt trên bề mặt phẳng và ổn định
Việc căn chỉnh bàn đỡ là một trong những bước quan trọng nhất, ảnh hưởng trực tiếp đến tỷ lệ thành công của quá trình in. Bàn đỡ quá gần có thể làm rách màng FEP, trong khi quá xa có thể dẫn đến lỗi bám dính.
Theo dõi quá trình in:
- Quan sát các lớp đầu tiên để đảm bảo bám dính tốt
- Kiểm tra tiến độ in qua cửa sổ quan sát hoặc camera (nếu có)
- Để ý đến các âm thanh bất thường có thể chỉ ra vấn đề về lực bám
- Duy trì nhiệt độ phòng ổn định (lý tưởng từ 22-25°C)
Mặc dù công nghệ DLP khá tự động, việc theo dõi các giai đoạn đầu của quá trình in rất quan trọng để phát hiện sớm các vấn đề tiềm ẩn và có thể can thiệp kịp thời.
Xử lý sau in:
Vệ sinh chi tiết:
- Tháo mô hình khỏi bàn đỡ và để ráo nhựa dư trong 10-15 phút
- Rửa mô hình trong cồn isopropyl (IPA) 91-99% trong 3-5 phút, tốt nhất là sử dụng máy rửa siêu âm
- Thực hiện rửa thứ hai trong IPA sạch nếu cần
- Để mô hình khô hoàn toàn trước khi gia cố UV
Quá trình rửa loại bỏ nhựa chưa đông cứng bám trên bề mặt mô hình. Việc không làm sạch đúng cách có thể dẫn đến bề mặt nhớp và giảm độ chính xác của chi tiết.
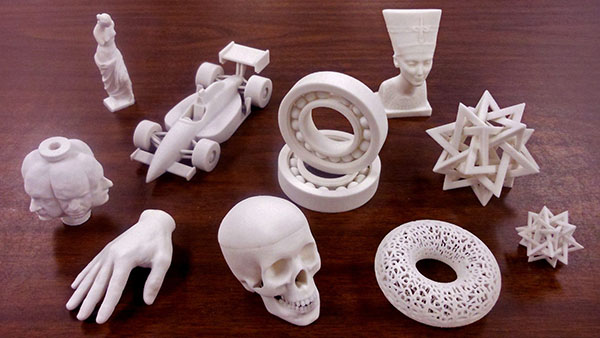
Tháo đế đỡ:
- Sử dụng kìm cắt nhỏ hoặc dao cắt để loại bỏ cấu trúc đỡ
- Cắt sát với bề mặt mô hình nhưng không làm hỏng chi tiết
- Đánh dấu các vị trí cần xử lý thêm sau khi gia cố UV
- Thu gom và xử lý đúng cách các phần thải
Cấu trúc đỡ dễ tháo hơn trước khi gia cố UV hoàn toàn, tuy nhiên mô hình cũng dễ bị biến dạng hơn. Cần cân nhắc giữa hai yếu tố này khi quyết định thời điểm tháo đế đỡ.
Xử lý bề mặt:
- Gia cố mô hình bằng UV trong 2-10 phút (tùy thuộc vào kích thước và loại nhựa)
- Xử lý các vết cắt bằng giấy nhám mịn (600-2000 grit)
- Đánh bóng bề mặt nếu cần thiết
- Sơn hoặc phủ lớp bảo vệ tùy theo ứng dụng
Việc gia cố UV đúng cách rất quan trọng để đạt được cường độ cơ học tối đa. Thời gian gia cố không đủ dẫn đến độ cứng thấp, trong khi thời gian quá dài có thể làm vật liệu giòn và dễ gãy.
Kiểm tra chất lượng:
- Đánh giá độ chính xác kích thước so với thiết kế gốc
- Kiểm tra tính toàn vẹn của các chi tiết nhỏ
- Đánh giá độ mịn và chất lượng bề mặt
- Thử nghiệm chức năng nếu chi tiết là thành phần cơ khí
Quy trình kiểm tra chất lượng giúp xác định các vấn đề tiềm ẩn và điều chỉnh các thông số in cho các lần in tiếp theo.
3.2 Các dòng máy in 3D DLP
Để chọn được máy in 3D DLP phù hợp, hãy tham khảo hướng dẫn chọn máy theo các tiêu chí đánh giá dưới đây của 3D Minion:
Tiêu chí đánh giá chất lượng máy in 3D cho công nghệ in DLP:
- Độ phân giải: Độ phân giải XY của máy in DLP phụ thuộc vào độ phân giải của chip DMD và hệ thống quang học
- Kích thước vùng in: Xác định kích thước tối đa của sản phẩm có thể in
- Tốc độ in: Phụ thuộc vào cường độ ánh sáng và hiệu suất hệ thống cơ khí
- Giá thành: Phản ánh chất lượng linh kiện và độ bền của thiết bị
- Khả năng tương thích vật liệu: Một số máy chỉ tương thích với nhựa của nhà sản xuất
- Phần mềm đi kèm: Ảnh hưởng đến trải nghiệm người dùng và chức năng
- Bảo hành và hỗ trợ kỹ thuật: Quan trọng với thiết bị công nghệ cao
So sánh các model phổ biến:
Model | Độ phân giải XY | Vùng in (mm) | Độ dày lớp | Tốc độ | Giá (USD) | Đặc điểm nổi bật |
Anycubic Photon M3 | 4K (3840×2400) | 163x102x180 | 0,01-0,15mm | 50mm/h | 300-400 | Giá rẻ, phù hợp người mới bắt đầu |
Elegoo Saturn 2 | 8K (7680×4320) | 219x123x250 | 0,01-0,1mm | 70mm/h | 500-600 | Vùng in lớn, độ phân giải cao |
Phrozen Sonic Mini 8K | 8K (7500×3240) | 165x72x180 | 0,01-0,1mm | 80mm/h | 600-700 | Độ phân giải siêu cao, tốc độ nhanh |
Formlabs Form 3+ | 2K (1440×1440) | 145x145x185 | 0,025-0,3mm | 30mm/h | 3500+ | Hệ sinh thái khép kín, độ tin cậy cao |
Peopoly Phenom L | 4K (3840×2160) | 345x194x400 | 0,05-0,3mm | 60mm/h | 2000-2500 | Vùng in cực lớn cho máy DLP |
Gợi ý 1 số dòng mày theo nhu cầu/ngân sách:
- Ngân sách dưới 500 USD: Anycubic Photon M3 hoặc Elegoo Mars 3 – Phù hợp cho người mới bắt đầu, có thể in các mô hình chi tiết nhỏ với chất lượng tốt
- Ngân sách 500-1000 USD: Elegoo Saturn 2 hoặc Phrozen Sonic Mini 8K – Cân bằng giữa chất lượng, tốc độ và kích thước vùng in, phù hợp cho người đam mê và doanh nghiệp nhỏ
- Ngân sách 1000-3000 USD: Peopoly Phenom hoặc UNIZ IBEE – Vùng in lớn, độ tin cậy cao, phù hợp cho sản xuất nhỏ và nguyên mẫu chuyên nghiệp
- Ngân sách trên 3000 USD: Formlabs Form 3+ hoặc EnvisionTEC Micro Plus HD – Chất lượng hàng đầu, được sử dụng trong ngành nha khoa, y tế và chế tạo chuyên nghiệp
Tips mua hàng:
- Xác định nhu cầu trước: Ưu tiên các thông số phù hợp với mục đích sử dụng cụ thể
- Kiểm tra chi phí vật liệu: Máy bắt buộc sử dụng nhựa riêng sẽ có chi phí vận hành cao hơn
- Tính toán tổng chi phí sở hữu: Bao gồm cả thiết bị hậu xử lý, vật tư tiêu hao và bảo trì
- Tìm hiểu cộng đồng hỗ trợ: Ưu tiên các thương hiệu có cộng đồng người dùng lớn và tích cực
- Xem xét khả năng nâng cấp: Một số máy cho phép nâng cấp phần cứng hoặc firmware để cải thiện hiệu suất
- Kiểm tra tính tương thích: Đảm bảo máy có thể sử dụng với phần mềm slicing phổ biến
4. So sánh các công nghệ in 3D Resin: SLA, DLP, LCD
Bảng so sánh nhanh 3 công nghệ in resin phổ biến nhất hiện tại:
Tiêu chí | SLA (Stereolithography) | DLP (Digital Light Processing) | LCD (Liquid Crystal Display) |
Nguồn sáng | Laser UV | Đèn UV/LED + Chip DMD | Màn hình LCD + Đèn UV/LED |
Nguyên lý hoạt động | Tia laser quét từng điểm | Chiếu sáng toàn bộ lớp cùng lúc qua chip DMD | Màn hình LCD chặn/cho ánh sáng đi qua |
Độ phân giải | Rất cao (10-25 micron) | Cao (25-50 micron) | Trung bình-cao (35-75 micron) |
Tốc độ in | Chậm | Nhanh (5-10x so với SLA) | Nhanh (tương đương DLP) |
Chi phí máy | Cao (3000-10000 USD) | Trung bình-cao (500-5000 USD) | Thấp (200-1000 USD) |
Kích thước vùng in | Lớn (đến 800x400mm) | Trung bình (đến 300x200mm) | Nhỏ-trung bình (đến 200x120mm) |
Độ chính xác | Tuyệt vời | Rất tốt | Tốt |
Vật liệu sử dụng | Đa dạng, đặc tính cao | Đa dạng, đặc tính cao | Hạn chế hơn, đặc tính thấp hơn |
Tuổi thọ thiết bị | Cao | Trung bình-cao | Thấp (LCD cần thay định kỳ) |
Chi phí vận hành | Cao | Trung bình | Thấp |
Phân tích chi tiết ưu nhược điểm của từng công nghệ in 3D resin:
1. Công nghệ SLA (Stereolithography)
Ưu điểm:
- Độ chính xác và chi tiết cao nhất trong các công nghệ in resin
- Bề mặt mịn màng với ít dấu vết của lớp in
- Khả năng sử dụng nhiều loại vật liệu đặc biệt
- Tuổi thọ thiết bị cao, chi phí bảo trì thấp trong dài hạn
Nhược điểm:
- Tốc độ in chậm do laser phải di chuyển và quét từng điểm
- Chi phí đầu tư và vận hành cao
- Nguồn laser thường đắt đỏ khi cần thay thế
- Phần mềm điều khiển phức tạp hơn
SLA là công nghệ lý tưởng cho các ứng dụng yêu cầu độ chính xác cực cao như nha khoa, trang sức, và chế tạo khuôn mẫu chính xác. Dù chi phí cao nhưng chất lượng sản phẩm vượt trội, đặc biệt với các chi tiết phức tạp.
2. Công nghệ DLP (Digital Light Processing)
Ưu điểm:
- Tốc độ in nhanh do chiếu sáng cả một lớp cùng lúc
- Cân bằng tốt giữa độ chính xác và tốc độ
- Độ phân giải cao, đặc biệt với các chip DMD hiện đại
- Khả năng xử lý cả các chi tiết phức tạp và mịn
Nhược điểm:
- Độ phân giải giảm ở các vị trí xa trung tâm do hiệu ứng quang học
- Giới hạn về kích thước vùng in so với SLA
- Chi phí trung bình-cao, đặc biệt với các máy chuyên nghiệp
- Chip DMD có thể bị hư hỏng theo thời gian
DLP là lựa chọn cân bằng giữa SLA và LCD, phù hợp cho các doanh nghiệp vừa và nhỏ, phòng thí nghiệm, và người đam mê muốn sản xuất các mô hình chất lượng cao với tốc độ tốt.
3. Công nghệ LCD (Liquid Crystal Display)
Ưu điểm:
- Chi phí đầu tư thấp nhất trong các công nghệ in resin
- Tốc độ in nhanh tương đương DLP
- Dễ sử dụng và bảo trì
- Phổ biến và có nhiều lựa chọn máy in
Nhược điểm:
- Độ phân giải và độ chính xác thấp hơn SLA và DLP
- Màn hình LCD cần thay định kỳ (thường sau 500-2000 giờ in)
- Ánh sáng kém đồng nhất ảnh hưởng đến chất lượng sản phẩm
- Hạn chế về khả năng sử dụng các vật liệu đặc biệt
LCD là lựa chọn phổ biến cho người mới bắt đầu và người đam mê với ngân sách hạn chế. Công nghệ này phù hợp với các mô hình trang trí, nguyên mẫu nhanh, và các ứng dụng không yêu cầu độ chính xác cực cao.
Công nghệ in 3D DLP đã và đang chứng minh giá trị to lớn của mình trong nhiều lĩnh vực từ y tế, trang sức, chế tạo đến giáo dục và thiết kế. Với những ưu điểm vượt trội về tốc độ, độ chính xác và khả năng tạo ra các chi tiết phức tạp, DLP đang dần trở thành lựa chọn phổ biến cho cả người đam mê và các doanh nghiệp.
Mặc dù vẫn còn những hạn chế về kích thước vùng in và chi phí đầu tư ban đầu, nhưng với tốc độ phát triển nhanh chóng của công nghệ và vật liệu, những rào cản này đang dần được vượt qua. Trong tương lai gần, chúng ta có thể kỳ vọng vào các máy in DLP có khả năng sản xuất các chi tiết lớn hơn, nhanh hơn và với nhiều loại vật liệu đa dạng hơn.
Cho dù bạn là người mới bắt đầu tìm hiểu về in 3D hay một chuyên gia đang cân nhắc đầu tư vào công nghệ mới, in 3D DLP chắc chắn là một công nghệ đáng để khám phá và tận dụng trong thời đại số hóa sản xuất hiện nay.